RCDTA Railwalk
Historic Preservation & Repair
Structural Challenge
Take a 150+ year old structure held together with suspension cables and turn it into a modern covered driveway/outdoor event space. Preserve and repair the original front masonry wall and create a monolithic, floating slab on top of suboptimal soil conditions. Those were just some of the major challenges facing our team during the RCTDA Railwalk project.
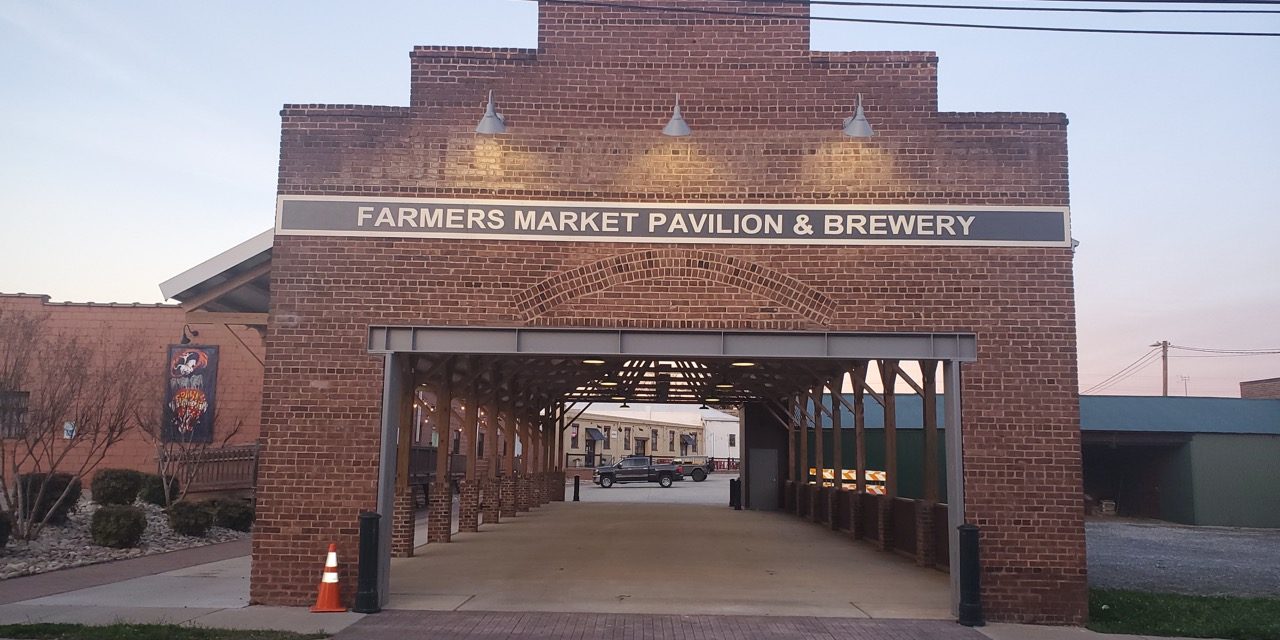
Saving the original, historic, front brick wall
We began this project by consulting with a team of structural engineers in order to develop a shoring plan to save the front masonry wall from the original building. Per local zoning requirements the original wall was required to be incorporated into the new structure. For that to happen we needed to provide enough support for the front wall to stand while new structural elements were installed behind the wall. Originally this temporary shoring would be required to stand for nearly 3 months. However, due to the presence of poor soils under the new building slab the temporary shoring remained in place for much longer.
Certified soil testing provided evidence of unsuitable soil conditions under the proposed building slab. Remediation of the unsuitable solid required removing up to 5 feet of the worst soil and shifting the design to incorporate a monolithic slab with micropiles. Micropiles essentially serve as a vertical bridge from the unsuitable soils near the surface to stronger soils deeper underground. Approximately 35 micropiles were installed on this project at an average depth of 40 feet. In order to accommodate point loading from the micropile caps the slab design was changed to include nearly 9 tons of rebar! Exterior footings and column footings were incorporated into the slab design creating a monolithic pour including over 100 yards of concrete.
The combination of steel and timber framing increased the focus on using the correct structural connectors and fasteners. Every column base and cap was designed to fit for the unique loading requirements of each column.
Finishing the project provided additional challenges. The metal imprinted panels on the knee wall side of the structure were repurposed from the original building and are well over 150 years old. Even relatively simple tasks such as installing signage and down lights on the front facade required additional tuck pointing of the original masonry wall. We used a mortar stain kit to improve the blend between new and old mortar. We used a concrete stamp with a color releasing agent so that the front driveway blended in with the adjacent sidewalk on the property.